Altering the type of rebar used in a construction project can be a significant undertaking, but it can be achieved satisfactorily with careful planning and execution. Understanding the reasons for the switch and the implications of using a different type of rebar are crucial. When considering a rebar type switch, factors such as strength, availability, cost, and compatibility with existing materials must be thoroughly evaluated. The goal is to ensure that the new rebar type meets the structural requirements and enhances the overall performance of the project.
Transitioning from one rebar type to another involves several steps. Firstly, a comprehensive assessment of the existing rebar and the proposed replacement is essential. This evaluation should consider the diameter, grade, and yield strength of the rebars, as well as their compatibility with the concrete mix design. Additionally, the availability and cost of the new rebar type should be taken into account. It is advisable to consult with engineers, suppliers, and contractors to gain insights and recommendations on the most appropriate rebar type for the specific project requirements.
Once the decision to switch rebar types has been made, it is crucial to communicate this change effectively to all stakeholders involved in the construction process. This includes architects, engineers, contractors, inspectors, and suppliers. Clear documentation, including updated drawings and specifications, should be provided to ensure that everyone is aware of the change and its implications. Furthermore, it is essential to establish a robust quality control process to verify that the new rebar type meets the specified requirements and is installed correctly. Regular inspections and testing should be conducted to ensure the integrity and performance of the structure.
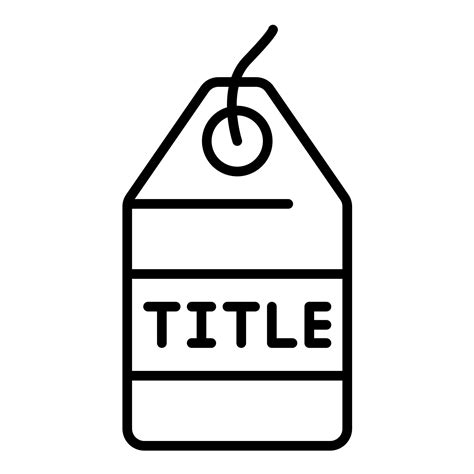
How To Switch Rebar Type Satisfactory
To switch rebar type in Satisfactory, you first need to unlock the MAM research for the new rebar type you want to use. Once you have unlocked the research, you can then go to a Constructor and select the “Switch Rebar Type” option. This will open up a menu where you can select the new rebar type you want to use. Once you have selected the new rebar type, the Constructor will begin producing the new type of rebar.
It is important to note that switching rebar types will require you to have the appropriate resources available. For example, if you want to switch to steel rebar, you will need to have steel plates available. You can also use the MAM research to unlock recipes for producing different types of rebar from different resources.
People Also Ask
How do I unlock new rebar types in Satisfactory?
You can unlock new rebar types in Satisfactory by completing MAM research. The MAM research tree is located in the HUB menu. Once you have unlocked the research for a new rebar type, you can then go to a Constructor and select the “Switch Rebar Type” option to begin producing the new type of rebar.
What are the different types of rebar in Satisfactory?
There are three different types of rebar in Satisfactory: iron rebar, steel rebar, and carbon fiber rebar. Iron rebar is the most basic type of rebar and is made from iron plates. Steel rebar is stronger than iron rebar and is made from steel plates. Carbon fiber rebar is the strongest type of rebar and is made from carbon fiber sheets.
Which type of rebar should I use?
The type of rebar you should use will depend on the specific application. If you need a strong and durable rebar for a large structure, then you should use steel rebar or carbon fiber rebar. If you need a more basic and affordable rebar for a smaller structure, then you can use iron rebar.