
There is nothing more frustrating than getting behind the wheel of your 2015 Chevrolet Tahoe and discovering the driver’s seat isn’t moving back as it should. To determine if the seat is the culprit, you first must ensure it’s receiving power. If the seat isn’t receiving power, the problem lies elsewhere. If the seat is receiving power, you can try swapping out the seat switch. However, if that doesn’t correct the problem, it’s likely the seat track has failed. 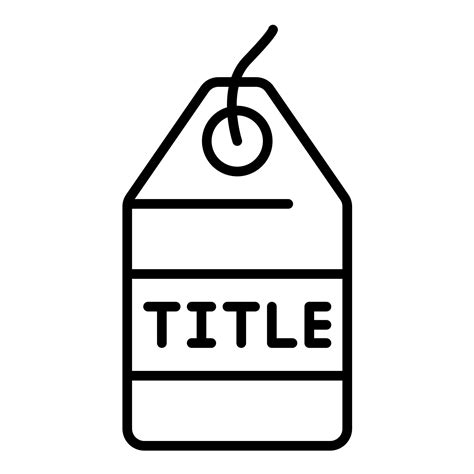
Replacing a seat track is a job best left to the professionals. However, if you’re handy with tools and have some mechanical experience, you can save yourself some money by doing it yourself. Here are the steps on how to replace the driver’s seat track in a 2015 Chevrolet Tahoe:
- Gather your tools and materials. You will need a set of metric wrenches and sockets, a Phillips head screwdriver, a flathead screwdriver, and a new seat track.
- Disconnect the battery. This will prevent any electrical accidents from occurring while you are working on the seat.
- Remove the seat. There are four bolts that hold the seat in place. Remove these bolts and lift the seat out of the vehicle.
- Disconnect the electrical connectors. There are two electrical connectors that need to be disconnected. One is for the seat belt and the other is for the seat.
- Remove the old seat track. There are four bolts that hold the seat track in place. Remove these bolts and lift the seat track out of the vehicle.
- Install the new seat track. Place the new seat track in the vehicle and line up the bolt holes. Insert the bolts and tighten them down.
- Reconnect the electrical connectors. Plug the seat belt and seat connectors back into the seat track.
- Install the seat. Lift the seat into the vehicle and line up the bolt holes. Insert the bolts and tighten them down.
- Reconnect the battery. Connect the negative terminal to the battery first, followed by the positive terminal.
Disconnecting the Seat Wiring
1. Locate the three wiring harnesses connected to the driver’s seat.
2. Carefully disconnect each wiring harness by pressing on the release tab and pulling the connector straight out.
3. Be gentle when disconnecting the harnesses, as rough handling can damage the wires or connectors.
4. The three wiring harnesses are:
Harness |
Description |
1 |
Connects to the seat motor, heated seat, and lumbar support |
2 |
Connects to the seat airbag and seat belt tensioner |
3 |
Connects to the seat position sensor |
5. Once all three wiring harnesses have been disconnected, the seat is now free to be removed from the vehicle.
Removing the Motor
1. Disconnect the negative battery terminal.
2. Remove the two bolts that secure the motor to the seat track. The bolts are located at the rear of the motor.
3. Unplug the electrical connector from the motor.
4. Remove the motor from the seat track.
5. Inspect the motor for damage. If the motor is damaged, it will need to be replaced.
6. To replace the motor, reverse the removal procedure. Be sure to connect the electrical connector to the motor before installing the bolts that secure the motor to the seat track.
Tools Needed |
Materials Needed |
10mm socket |
New seat track motor |
Phillips screwdriver |
|
Aligning the Seat Rail
To properly align the seat rail, it’s crucial to ensure that the rail is correctly positioned before tightening the bolts. Here’s how to do it step by step:
- Position the Seat: Place the seat on top of the newly installed track, ensuring that it’s aligned properly and fully seated on the track.
- Check Alignment: Inspect the front and rear of the seat to verify that it’s aligned straight and parallel to the vehicle’s floor.
- Test Movement: Manually move the seat forward and backward to ensure smooth operation and ensure it doesn’t bind or stick.
- Adjust Position: If necessary, make minor adjustments to the seat position by loosening the bolts, shifting the seat, and retightening the bolts.
- Tighten Bolts: Once satisfied with the alignment, sufficiently tighten the bolts to secure the seat securely.
- Check Alignment Again: Double-check the alignment by moving the seat again to ensure it remains straight and parallel.
- Final Inspection: Inspect the entire seat assembly, including the track, bolts, and seat movement, to ensure everything is functioning correctly.
- Final Tightening: Once you’re satisfied with the alignment and operation, fully tighten all the bolts to secure the seat permanently.
Bolt Size |
Torque Specification |
Front Mounting Bolts |
48 ft-lbs |
Rear Mounting Bolts |
48 ft-lbs |
Remember, it’s essential to follow the specified torque values when tightening the bolts to ensure proper seat stability and prevent any potential issues down the road.
Reinstalling the Seat Bolts
Once the seat track is securely attached, it’s time to reinstall the seat bolts. These bolts hold the seat to the track, ensuring it remains stable and secure during use. Follow these steps to reinstall the seat bolts:
- Locate the seat bolts at the front and rear of the seat track.
- Use a torque wrench to tighten the front bolts to the specified torque value.
- Tighten the rear bolts to the same torque value as the front bolts.
- Confirm that all seat bolts are securely tightened.
Note: Refer to your vehicle’s service manual for the specific torque values for the seat bolts.
Seat Bolt Location |
Torque Value (ft-lbs) |
Front |
[Front bolt torque value] |
Rear |
[Rear bolt torque value] |
Once the seat bolts are tightened, you have successfully replaced the driver seat track on your 2015 Chevy Tahoe. Double-check the stability of the seat by gently rocking it back and forth to ensure it’s secure and moves smoothly along the track.
How To Replace 2015 Chevy Tahoe Driver Seat Track
The driver seat track is a crucial component of the vehicle’s seating system, responsible for adjusting and securing the driver’s seat position. In the case of a 2015 Chevy Tahoe, if the seat track becomes faulty or damaged, it can lead to discomfort, safety hazards, and difficulty using the vehicle. Fortunately, replacing the driver seat track on a 2015 Chevy Tahoe is a feasible task that can be accomplished with proper tools and a step-by-step guide.
To effectively replace the driver seat track, it’s essential to follow the recommended procedures and utilize the appropriate components. General guidelines involve disconnecting the battery, removing the seat, detaching the seat belt buckle and pretensioner, unbolting the seat track, installing the new track, and reassembling the components in reverse order.
Safety precautions should be prioritized throughout the process, including wearing appropriate protective gear and using the correct tools for each step. Detailed instructions and any necessary diagrams or illustrations will be provided to assist in the successful replacement of the 2015 Chevy Tahoe driver seat track.
People Also Ask About How To Replace 2015 Chevy Tahoe Driver Seat Track
What are the signs of a faulty seat track?
Common symptoms of a faulty seat track may include difficulty adjusting the seat position, excessive play or movement of the seat, and unusual noises or vibrations while adjusting the seat.
What tools are required for this replacement?
The necessary tools for replacing a 2015 Chevy Tahoe driver seat track typically include a set of wrenches, sockets, a torque wrench, a pry bar, and possibly a seat track removal tool.
Is it possible to repair a damaged seat track instead of replacing it?
While it may be possible to repair some types of seat track damage, replacing the entire track is generally recommended for optimal safety and functionality. Repairs may not always be reliable or as effective as using a new track.